Published in The Daily Record: December 30th, 2013 by Lizzy McLellan
Wind farms require windmills, and windmills require welders.
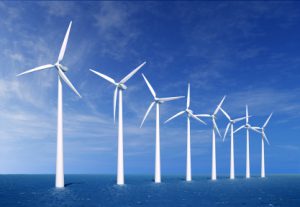
This simple realization — it came up at a dinner in June when the state was discussing the Danish government’s experience with offshore wind power — struck motivation into three companies that are planning for wind farms off the coast of Maryland.
The result: a planning grant that will help Humanim, D&T Welding Contractor and Cianbro train a workforce of welders for the future.
The three recruited more partners: Earlbeck Gases and Technologies, the Maritime Applied Physics Corp., the Worcester County Economic Development Office, the Maryland Center for Construction Education and Innovation and Anne Arundel Community College. They applied for the grant together, as the Maryland Offshore Wind Strategic Industry Partnership. And they were one of 29 winners from biotech to cybersecurity that secured a total of more than $600,000 from the state for planning. The partnership’s share was $24,000.
Liz Burdock, executive director of the Business Network for Maryland Offshore Wind, an organization with dozens of partners interested in offshore wind development, was in on the application process.
“They’re having to pass up some business opportunities because they don’t have the workforce in place,” Burdock said of the welding firms. “They can’t employ enough good, trained welders.”
It’s not only a workforce issue, but also an obstacle to energy innovation. So when the alliance heard of the state’s EARN grant program, administered by the Maryland Department of Labor, Licensing and Regulation, it seemed like a natural opportunity. EARN stands for Employment Advancement Right Now; it aims to fill this and other skills gaps in Maryland by funding the planning and implementation of workforce training programs.
All EARN applicants were required to be partnerships, with at least two employers and two related organizations. The winners were announced Monday, and implementation grant proposals are due in March, to be awarded in May.
The Maryland Offshore Wind Strategic Industry Partnership was already planning to fill the welder training need, said Burdock, but the EARN grant will move it along.
The partnership’s idea, to be developed with the planning grant, is to use current welding opportunities as training for the future windmill fabrication needs.
“It’s innovative,” said Elisabeth Sachs, who runs the EARN program for DLLR. “They’re basically looking way into the future.”
Welding companies already need workers to create large infrastructure assemblies, said Burdock, like bridge and building parts. By training the workforce for these jobs, they can also provide the skills needed to create a windmill.
“We were looking at the shortage of welders today, but then also training with an eye on the future,” she said.
The benefits apply to welders of smaller pieces as well, said Burdock. They will know how to make the smaller parts of the windmills, like ladder steps.
The entire training plan is not yet on paper, she said. That’s what the grant is for. It will allow for a better understanding of what each partner needs and what the current obstacles are.
It’s not just the grant money, but also facilitating partnerships, that benefits the awardees, said Scott Jensen, deputy secretary at DLLR. Since small firms in Maryland already weld, he said, wind farms present an opportunity for them to grow with the right planning.
“What EARN wants to do is form the partnerships with the players that are going to need to work together to allow the pipeline to build,” said Jensen. “There’s no windmills to weld at the moment … [but] we don’t have to wait to sort of build a farm team for the wind farms.”